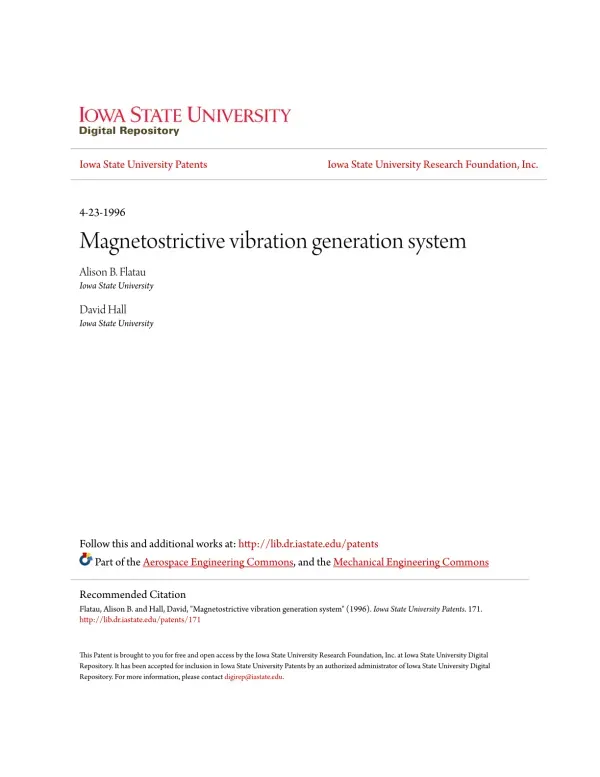
Magnetostrictive Vibration System
Document information
Author | Alison B. Flatau |
School | Iowa State University |
Major | Aerospace Engineering |
Document type | Patent |
Language | English |
Format | |
Size | 1.82 MB |
Summary
I.Magnetostrictive Vibration Generation System Patent Overview
This patent (US Patent 5,510,660, April 23, 1996) describes a novel magnetostrictive vibration generation system utilizing a Terfenol-D rod actuator. Inventors Alison Flatau and David Hall of Iowa State University developed this shaker, which features a mass coupled to the actuator via spring mechanisms, ensuring a constant air gap during vibration. The actuator is housed within a cylindrical coil and permanent magnet assembly. An electrical drive system provides the excitation signal, causing the Terfenol-D rod to vibrate. Key features include an optional vibrating mass on one end and an implantable version incorporating a Biomer™ coating and leak-proof seal for in-vivo testing of tissue response to specific vibrations. The system also includes a pre-stress adjusting screw for precise control. The patent builds upon prior work detailed in several cited publications, including those focusing on the design of lanthanide magnetostrictive sonar projectors and the application of Terfenol-D in various actuators.
1. Core Technology and Device Description
The patent centers on a magnetostrictive vibration generation system, specifically a novel shaker design. The core component is a Terfenol-D rod actuator, a magnetostrictive material known for its ability to convert magnetic energy into mechanical vibrations. This actuator is ingeniously coupled to a mass at both ends through a precisely engineered system of spring seats, a spring seat/adjuster, and a spring washer. This arrangement is crucial for maintaining a consistent annular coaxial air gap, ensuring stable and reliable performance even under significant vibration. The entire assembly is housed within a cylindrical coil situated inside a permanent magnet, which itself is housed in a cylindrical housing. An electrical drive system supplies a predetermined excitation signal to the coil, inducing a magnetic field that, in turn, drives the Terfenol-D rod to vibrate at a precise frequency. The design prioritizes control and efficiency in vibration generation.
2. Embodiments and Applications Standard and Implantable Shakers
The patent outlines multiple embodiments of this magnetostrictive vibration generation system. A primary embodiment details a standard shaker design, highlighting the precise control offered by the spring-based mass coupling and consistent air gap. The system's ability to generate precise, controlled vibrations is a key aspect of this design. However, the patent's most innovative aspect is the introduction of an implantable shaker. This embodiment is specifically engineered for in-vivo applications, including biomedical research. Critical to its functionality is the inclusion of a leak-proof seal and a Biomer™ coating, both necessary for biocompatibility and reliable operation within a living organism. This implantable design opens possibilities for experiments involving tissue response to controlled vibrations, providing a significant advancement in biomedical research tools. This highlights the versatility of the underlying Terfenol-D actuator technology.
3. Design Details and Mechanisms for Enhanced Performance
Several design features contribute to the improved performance of this magnetostrictive vibration generation system. The use of a Terfenol-D rod actuator is central, leveraging its unique magnetostrictive properties for efficient energy conversion. The spring-based system of mass coupling not only enhances stability but also maintains a constant air gap between the spring base and spring seat. This constant gap ensures consistent vibration characteristics regardless of the actuator's movement. Additionally, the inclusion of a pre-stress adjusting screw allows for precise control over the system's operating parameters. These design choices are significant and directly impact the precision and efficiency of the generated vibrations, showcasing a considered approach to engineering a high-performance shaker using a Terfenol-D actuator. The entire design, from the actuator to the housing, is optimized for efficient vibration generation and control.
4. Patent Number Inventors and Assignee
This invention, a magnetostrictive vibration generation system, is officially documented under US Patent number 5,510,660, granted on April 23, 1996. The inventors are listed as Alison Flatau and David Hall, both researchers affiliated with Iowa State University in Ames, Iowa. The patent is assigned to the Iowa State University Research Foundation, Inc., also located in Ames, Iowa. This demonstrates a clear connection between academic research at Iowa State University and the development and commercialization potential of this novel shaker technology utilizing a Terfenol-D actuator. The system focuses on precise and efficient vibration generation.
II.Key Embodiments and Applications
The patent details several embodiments of the magnetostrictive vibration generation system. One embodiment focuses on a standard shaker design emphasizing precise control and consistent performance. A second crucial embodiment highlights an implantable shaker, designed for biocompatibility and leak-proof operation. This version allows for testing tissue response to controlled vibrations in animal models. Both configurations leverage the unique properties of Terfenol-D for efficient vibration generation.
1. Standard Shaker Embodiment Design and Functionality
One key embodiment of the patented magnetostrictive vibration generation system describes a standard shaker design. This design emphasizes precise control over vibration generation. The core of this design, like all embodiments, is the Terfenol-D rod actuator. The actuator's movement is managed by a system of springs—a spring seat, a spring seat/adjuster, and a spring washer—which work together to maintain a consistent annular coaxial air gap. This air gap remains constant even when the rod vibrates, ensuring reliable and consistent vibration output. The actuator resides within a cylindrical coil, itself enclosed within a cylindrical permanent magnet, and finally, a protective cylindrical housing. An external electrical drive system delivers the excitation signal, resulting in controlled vibrations from the Terfenol-D rod. The shaker's design highlights the precision and stability achievable with the patented system.
2. Implantable Shaker Embodiment Biomedical Applications
A particularly significant embodiment is the implantable shaker. This design caters to biomedical applications, notably in vivo testing of tissue response to controlled vibrations. A major advancement in this design is its biocompatibility. The implantable shaker incorporates a leak-proof seal and a Biomer™ coating. The seal prevents leakage, while the Biomer™ coating ensures the device is safe for implantation. The ability to implant this shaker and observe the effects of specific vibrations on animal tissues provides a powerful research tool. This embodiment leverages the core technology of the Terfenol-D rod actuator, but adapts it for a vastly different application, demonstrating the versatility and potential impact of the magnetostrictive vibration generation system.
3. Additional Design Features Across Embodiments
Beyond the standard and implantable versions, the patent describes design features common to all embodiments of the magnetostrictive vibration generation system. A key feature is the pre-stress adjusting screw. This screw, threaded into the end of the housing and secured with a jam nut, allows for fine-tuning of the Terfenol-D rod actuator's position. This adjustment is important for optimizing performance and maintaining the consistent air gap crucial for controlled vibrations. The spring base, seated on one end of the actuator, further contributes to this consistent air gap, moving coaxially with the spring seat during operation. This design philosophy, incorporating features for precise adjustment and consistent functionality, is a hallmark of this patent and ensures reliable vibration generation in various contexts.
III.Technical Specifications and Components
The core of the invention is the Terfenol-D rod actuator, which is the heart of the magnetostrictive vibration generation system. The design incorporates a spring seat, spring seat/adjuster, and spring washer for precise control and consistent air gap maintenance during operation. The actuator is encased in a cylindrical coil situated inside a permanent magnet, all housed within a protective cylindrical housing. The system requires an external electrical drive system to provide the necessary excitation signal. The implantable shaker adds a seal for biocompatibility and a Biomer™ coating.
1. The Terfenol D Rod Actuator Core Component
The heart of the magnetostrictive vibration generation system is the Terfenol-D rod actuator. This actuator is a crucial component responsible for converting magnetic energy into mechanical vibrations. Its magnetostrictive properties are central to the system's functionality. The patent carefully details the actuator's integration within the overall design, highlighting its role in producing controlled vibrations. The Terfenol-D material's characteristics are implicitly crucial to the effectiveness of the entire device, as its ability to respond to magnetic fields is what drives the vibration generation process. The rod's physical dimensions and its interaction with other components are key technical specifications influencing the system's performance and the resulting vibrations.
2. Spring Mechanisms Ensuring Precise Control and Consistent Air Gap
To ensure precise control and consistent performance, the Terfenol-D rod actuator is integrated with a sophisticated spring system. This system comprises a spring seat, a spring seat/adjuster, and a spring washer. These components work in concert to maintain a consistent annular coaxial air gap between the spring base and spring seat. This constant air gap is critical for stable and predictable vibration output, preventing inconsistencies that might arise from changes in the relative positions of the components during operation. The precise engineering of these spring mechanisms is a key element in the patented design, ensuring the reliability and efficiency of the vibration generation process.
3. Housing and Electrical System Encapsulation and Excitation
The Terfenol-D rod actuator, along with the spring mechanisms, is carefully housed within a layered structure. The assembly is first encased in a cylindrical coil, then within a cylindrical permanent magnet, and finally within a cylindrical housing. This layered structure provides both protection and optimized magnetic field generation. An external electrical drive system is responsible for delivering a predetermined excitation signal to the coil. This electrical signal is crucial for inducing the magnetic field that interacts with the Terfenol-D rod, thereby driving the vibration generation process. The design of the housing and the electrical system are integrated aspects of the overall system's functionality, working together to maximize the efficiency and precision of the vibration generation process.
4. Implantable Shaker Modifications Biomer Coating and Seal
The implantable shaker embodiment introduces additional components crucial for biocompatibility. These include a seal to ensure leak-proof operation within a living organism and a Biomer™ coating on the device's exterior. The seal prevents fluid ingress, ensuring reliable performance in physiological environments. The Biomer™ coating enhances biocompatibility, reducing the potential for adverse reactions. These modifications demonstrate an understanding of the specific challenges of biomedical applications, adapting the core magnetostrictive vibration generation system for in-vivo use. The choice of materials directly impacts the system's suitability for implantation, representing a significant aspect of the implantable shaker's technical specifications.
IV.Prior Art and Related Research
The patent cites several prior art publications, demonstrating the inventors' understanding of the existing landscape in magnetostrictive technology and its application in vibration generation. These references cover topics such as the design of lanthanide magnetostrictive sonar projectors and application manuals for Terfenol-D transducers. The cited works provide a context for the innovation presented in the patent, highlighting the advancement and unique aspects of the developed shaker design.
1. Relevant US Patents Building Upon Existing Technology
The patent acknowledges prior art in the field of magnetostrictive vibration generation. Specifically, it references two US Patents: US Patent 4,749,891 (Sheng, June 1988) and US Patent 5,184,037 (Kobayashi et al., February 1993). While the specific details of these patents aren't provided, their citation indicates that the current invention builds upon and improves existing magnetostrictive technologies. This acknowledgement positions the innovation within a broader technological context, highlighting the advancement made by the current patent's vibration generation system. The listed patents provide a baseline for understanding the existing state of the art in the field of magnetostrictive actuators and vibration generation.
2. Other Publications Exploring Design and Applications of Terfenol D
The patent extensively references various publications that explore the design, application, and properties of Terfenol-D, the key material in the patented magnetostrictive vibration generation system. These references include conference proceedings, brochures from companies like ABB Seatech AS and Magespro S.A., and journal articles. The cited works cover diverse aspects of Terfenol-D, from its use in sonar projectors (“Design of Lanthanide Magnetostrictive Sonar Projectors,” Clayssen et al.) to its application in underwater loudspeakers and high-force linear actuators. The breadth of cited publications demonstrates the inventors' thorough understanding of the existing research and applications related to Terfenol-D and its potential for vibration generation. These references provide a context for the current innovation, showcasing its advancements within established research areas relating to magnetostrictive materials and devices.
3. Key Research Themes in Cited Publications
The publications cited in the patent reveal several key research themes relevant to the patented magnetostrictive vibration generation system. These themes include the design and development of high-performance Terfenol-D transducers (“Application Manual for the Design of Etrema Terfenol-D Magnetostrictive Transducers,” Butler), the active control of vibration using magnetostrictive Terfenol (“Attenuation and Transformation of Vibration Through Active Control of Magnetostrictive Terfenol,” Hiller et al.), and the material characterization of Terfenol-D for use in sensors and actuators (“Development and Characterization of Terfenol-D for Use in Sensors and Actuators,” Jiles). These themes highlight the ongoing research efforts focused on improving the performance, controllability, and diverse applications of magnetostrictive materials, providing a backdrop against which the innovation of the current patent can be fully appreciated in the field of vibration generation.
V.Inventors and Assignee
The inventors are Alison Flatau and David Hall, both affiliated with Iowa State University in Ames, Iowa. The assignee of the patent is the Iowa State University Research Foundation, Inc., also located in Ames, Iowa.
1. Inventors of the Magnetostrictive Vibration Generation System
The patent for the magnetostrictive vibration generation system lists two inventors: Alison Flatau and David Hall. Both inventors are explicitly identified as being from Ames, Iowa, and affiliated with Iowa State University. This connection to a specific university highlights the academic origins of the technology, suggesting a foundation in research and development. The inventors' affiliation with Iowa State University provides context and indicates a potential link between academic research and practical applications of the patented vibration generation system utilizing a Terfenol-D actuator. The inventors' location in Ames, Iowa, provides geographical context for the invention's development.
2. Assignee Iowa State University Research Foundation Inc.
The assignee of the patent is the Iowa State University Research Foundation, Inc., also located in Ames, Iowa. This indicates that the foundation holds the intellectual property rights to this magnetostrictive vibration generation system. The Research Foundation's role is significant because it suggests a mechanism for commercialization and technology transfer from the university setting to potential industrial applications. The Research Foundation's location in Ames, Iowa, further reinforces the connection between the university, the inventors, and the patented technology. The Research Foundation's involvement implies potential licensing opportunities and commercial viability for the novel shaker design, a crucial aspect of transitioning the research into practical vibration generation applications.