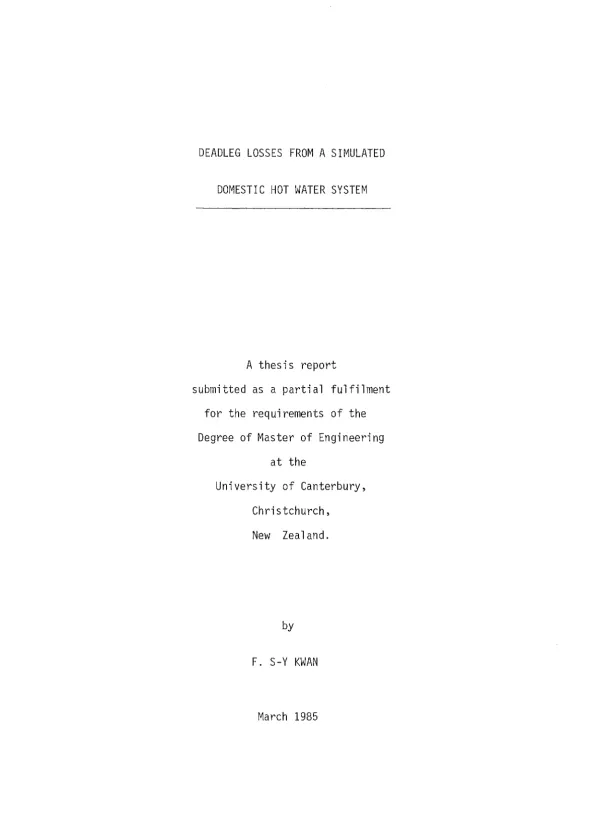
Deadleg Losses in Hot Water Systems
Document information
instructor | Dr. G. J. Parker |
School | University of Canterbury |
Major | Mechanical Engineering |
Place | Christchurch, New Zealand |
Document type | thesis |
Language | English |
Format | |
Size | 2.43 MB |
Summary
I.Experimental Setup for Simulating Deadleg Losses in Domestic Hot Water Systems
This research experimentally simulated deadleg losses in a domestic hot water system. A simulation rig, modified to accurately reflect real-world conditions, used forced convection to mimic natural convection heat transfer in pipes. The rig incorporated 5 sections of 75 mm ID PVC air 'tunnels' built over horizontal copper hot water pipes. Cool air, supplied by an air-conditioning unit at approximately 10°C, was blown through these tunnels to simulate the lower ambient temperatures encountered in a house. The system included various sensors, including thermocouples and platinum resistance thermometers, to monitor temperatures and flow rates, with data logged every 10 minutes (or 20 seconds during hot water draw-off). The experimental setup aimed to quantify heat loss in deadlegs under different water usage patterns and tank temperatures (70°C and 50°C were used).
1. Simulation Rig Overview and Objective
The core of the experiment was a domestic water system simulation rig, designed to measure deadleg losses. The primary goal was to simulate the daily heat losses from hot water pipes in a typical house, where ambient temperatures are significantly lower than room temperature (experiment conducted with ambient temperature low and room temperature at 18°C). This was achieved by using an air-conditioning unit to create a controlled environment, forcing cool air through PVC tunnels encasing the horizontal copper hot water pipes. This setup allowed for the experimental quantification of deadleg losses under various conditions, which are energy losses in the pipe sections that are not actively used at any given time. The experimental setup allowed for the investigation of heat loss under different water usage patterns and tank temperatures, enabling quantitative analysis of the impact of these variables on energy efficiency. The study focused on the impact of the ambient temperature and natural convection heat transfer in the domestic hot water system, which was effectively simulated using forced convection heat transfer.
2. Forced Convection System Design PVC Air Tunnels and Air Conditioning
To mimic the natural convection heat transfer within building structures, the rig utilized five sections of 75 mm ID PVC air 'tunnels'. These tunnels were strategically positioned around the horizontal copper hot water pipes, enabling the passage of cool air. An air-conditioning unit was employed to provide a controlled stream of cool air (approximately 10°C) to these tunnels. This process of forced convection heat transfer successfully simulated the effect of low ambient temperatures on the heat loss from the hot water pipes. The design of the PVC air tunnels ensured that the cool air was effectively distributed across each section of pipe, maintaining a consistent temperature gradient. The system provided for independent parallel flow heat exchangers, using 64 mm I.D. ‘Dunlopflex’ flexible hoses to connect the air-conditioning unit to the tunnels, ensuring uniform airflow and maximizing the efficiency of the heat loss simulation.
3. Instrumentation and Data Acquisition Sensors and Data Logging
Precise measurement of temperatures and flow rates was crucial. Multiple copper-constantan thermocouples were strategically placed along each pipe section (inlet, middle, and outlet) to capture temperature gradients and determine the average water temperature. Additional thermocouples monitored the storage tank outlet temperature. These thermocouples were linked to a digital millivoltmeter via a manually controlled switch. Water flow rates were measured using dial readouts or pulse-generating Hall Effect transducers. A data logger with 16 analog and 8 digital channels recorded the data. The data logger captured temperature data (from the platinum resistance thermometers) as voltage readings, later converted to temperature in the analysis program. Digital channels recorded flow rate pulses, scan times, and electricity usage (via a light sensor on the kWh meter). This comprehensive system provided a high-resolution record of the heat transfer process, vital for the analysis of deadleg losses under different conditions. The data logger was configured to scan channels every 10 minutes, switching to a 20-second scan rate during periods of hot water usage to capture dynamic changes in temperature and flow.
4. Control System and Experimental Parameters
The experiment was controlled by a microprocessor, enabling 24-hour operation. An SD System ZBO starter kit managed the hot water simulation rig, using Motortrol valves to regulate hot and cold water inflow and outflow at various user devices (basin, sink, washing machine, bath, and shower). The system incorporated level sensors to detect water level changes, and LM334 temperature transducers measured temperature changes at each device (excluding the washing machine). The hot water simulation rig was set up to operate under different experimental conditions, using two distinct water usage patterns (average and high) and tank temperatures of 70°C and 50°C to assess the impact of these parameters on heat losses. The experiment used a 24-hour data acquisition scheme. The data acquisition and control system played a critical role in ensuring accurate and comprehensive data collection. The automated control system allowed for the precise monitoring of the experiment over extended periods, simulating realistic usage patterns. The detailed data acquisition ensured that the research yielded accurate and reliable data on heat loss.
II.Modifications to the Simulation Rig for Accurate Deadleg Loss Measurement
To improve the accuracy of heat loss simulation, the existing rig underwent significant modifications. The original polybutylene pipes were replaced with copper pipes for better surface temperature measurement and controlled heat transfer. The addition of the PVC air tunnels, along with the use of an air-conditioning unit, allowed for the precise simulation of forced convection cooling, mimicking the natural convection heat transfer occurring in a real house. Insulation was added to minimize extraneous heat losses from the system. The modifications focused on the main horizontal transmission lengths of the rig, with a specific focus on section TK-J1, which received particular attention in terms of insulation and modifications to ensure correct water quantity and heat loss measurements.
1. Pipe Material Replacement Enhancing Heat Transfer Measurement
A key modification involved replacing the existing 'Qest-Dux' polybutylene pipes with copper pipes. This change was crucial for improving the accuracy of the experiment. Copper, unlike polybutylene, allows for more reliable surface temperature measurements, providing a better indication of the internal water temperature. This is because copper has higher thermal conductivity; therefore, the surface temperature is a more accurate reflection of the water temperature. The improved heat transfer characteristics of copper also simplified the control of heat transfer during the experiment, reducing the influence of variables that are difficult to measure or control within the experiment. The substitution directly enhanced the reliability of the heat loss measurements and therefore was a crucial step in improving the experiment's ability to quantify deadleg losses.
2. The Introduction of PVC Air Tunnels Simulating Building Fabric Effects
To accurately simulate the heat losses experienced by hot water pipes within the fabric of a building, the researchers introduced five sections of 75 mm I.D. PVC air tunnels. These tunnels were carefully constructed around the horizontal copper hot water pipes, allowing for a controlled flow of air. The design aimed to replicate the natural convection heat transfer that occurs in real-world situations where pipes are embedded in walls, floors, or ceilings and are exposed to significantly lower ambient temperatures. The air tunnels are a key element of simulating the thermal environment of a house, which provided for more accurate simulation of deadleg losses. By controlling the air temperature within the tunnels, the researchers were able to precisely adjust the rate of heat transfer from the pipes, enhancing the experiment’s ability to model real world conditions. The use of these tunnels, in combination with the controlled air temperature provided by the air-conditioning unit, substantially improved the accuracy of the deadleg loss simulation.
3. Insulation Measures Minimizing Extraneous Heat Loss
To minimize unwanted heat losses that could compromise the accuracy of the measurements, several insulation strategies were employed. All exposed junction points between the thermocouples and copper pipes were carefully covered with a thermal insulator. This step minimized the impact of localized temperature changes at the sensor-pipe interfaces, improving the overall accuracy of the temperature readings. For section TK-J1, the length from TK to 0 received extra insulation treatment using “Insultube” rigid urethane foam sleeving. This focused insulation minimized heat loss from that specific section, enabling a more precise analysis of heat loss in the other parts of the system. These careful insulation measures ensured that the measured heat losses were primarily attributable to deadleg effects and not external factors, thus improving the experiment's overall reliability and accuracy.
4. Airflow Control and System Fine Tuning
The researchers utilized a concentric tube parallel flow heat exchanger system for the simulation during periods of stationary water in the copper pipes. Calculations for the required airflow rate were done to achieve the necessary heat loss levels based on forced-convection heat transfer. The system required careful calibration; preliminary tests showed the air conditioner could produce three times the required airflow. However, the cooling rates needed adjustment to align with the calculated natural convection heat loss over a 24-hour period, accounting for the differences between natural and forced convection. To achieve this, a 'fine-tuning' process was undertaken using an average water usage pattern and tank thermostat settings of 70°C and 50°C. By monitoring the middle thermocouple of each pipe section over 24 hours, the system's performance was adjusted to accurately replicate calculated heat losses. This fine-tuning process ensured the experimental results accurately reflected the predicted heat losses under the different conditions.
III.Data Acquisition and Analysis of Heat Losses
The experiment employed a microprocessor-controlled system with a data logger to record temperature and flow rate data. Nine analog channels monitored temperatures using platinum resistance thermometers, and digital channels recorded flow rates (using Hall Effect transducers), time, and electricity consumption. The collected data was then analyzed using a dedicated program on an HP 82100A computer. This program calculated various energy quantities, including energy in hot water from the tank, energy at each device, changes in tank energy storage, and electrical input. The analysis distinguished between periods with flowing water (near-constant pipe temperature) and cooling periods. This allowed for the determination of both steady-state and transient heat losses.
1. Data Logging System Temperature and Flow Rate Measurement
The experimental setup employed a sophisticated data logging system to capture comprehensive data. A data logger, equipped with 16 analog and 8 digital channels, was the central component. Nine analog channels were used to monitor temperatures using platinum resistance thermometers, recording temperature values as voltage readings that were later converted into temperature readings using a dedicated program. The system used a master timer to scan channels every 10 minutes, switching to a 20-second scan rate when hot water was drawn off. This setup ensured that both steady-state and transient heat loss data were captured. The digital channels measured water flow rates, using either dial readouts or pulse-generating Hall Effect transducers, capturing the number of pulses to quantify flow rates. These channels also monitored the time of each scan and electricity consumption, via a light sensor on the kWh meter, allowing for a holistic view of the energy consumption and heat loss dynamics during the experiment. This multi-faceted approach to data acquisition provided a rich dataset for the subsequent analysis of heat transfer dynamics.
2. Data Analysis Calculation of Energy Quantities and Heat Losses
The data collected by the data logger was meticulously analyzed using a dedicated program on the Department's HP 82100A computer. The program converted digital information into real-world parameters and calculated key energy quantities. These included the energy in hot water drawn from the tank, energy in hot water at each device, the change in tank-stored energy, and the total electrical input. This comprehensive analysis provided a detailed picture of energy flows within the system. The analysis method differentiated between periods of water flow (where pipe temperature remained relatively constant) and cooling periods (where significant heat loss occurred). By analyzing the data in this way, the researchers were able to accurately quantify the heat losses associated with different phases of water usage within the system. This distinction was crucial in understanding the contribution of different factors to the overall energy consumption of the domestic hot water system. The calculated energy quantities were then used to determine the heat losses related to deadleg lengths within the system.
3. Analysis of Cooling Curves and Heat Transfer Coefficients
The analysis involved using experimental cooling curves to determine heat transfer coefficients under different conditions. For example, calculating cooling time intervals for every 10°C temperature drop from 70°C to 14°C required obtaining average deadleg heat loss values at average water temperatures from the curves. The heat transfer coefficient was calculated at various stages of the cooling process using experimental cooling curves and the method outlined previously. The analysis distinguished between heat losses associated with stationary water (deadleg losses) and flowing water. This differentiated approach allowed for a precise quantification of the energy losses attributable specifically to deadleg sections of the pipework. These data were used for further analysis to quantify the effects of changing variables like water usage patterns and tank temperatures on the rate of heat loss from the system. The results from the cooling curves enabled the researchers to refine their understanding of the heat transfer processes under the experimental conditions.
IV.Comparison of Calculated and Experimental Deadleg Losses
The research compared calculated deadleg losses (using established heat transfer equations and the measured data) with experimentally determined losses. This comparison was performed for different water usage patterns (average and high) and tank temperatures (70°C and 50°C). The results showed that a significant proportion of the total system heat loss (up to 46%) originated from areas outside the simulated deadleg system. Differences between calculated and experimental results were within acceptable limits, with the largest discrepancy being 10% for a specific pipe section. The analysis also considered the effects of varying heat transfer coefficients in natural and forced convection scenarios.
1. Methodology for Comparing Calculated and Experimental Heat Losses
The research compared calculated and experimentally determined daily deadleg losses in a domestic hot water system. The calculated losses were determined using established heat transfer equations, while experimental losses were derived from the collected data. This comparison was conducted under varying conditions, including different water usage patterns (average and high) and initial tank temperatures (70°C and 50°C). The analysis involved examining both the total daily energy losses and the losses per meter of pipe length. For each pipe section, calculated and experimental daily heat losses were compared. This detailed comparison aimed to validate the accuracy of the experimental setup and the applied heat transfer models. The results from this comparison helped assess the effectiveness of the simulation rig in accurately modeling deadleg losses within a real-world domestic hot water system.
2. Results and Analysis of Deadleg Heat Losses
The comparison of calculated and experimental daily deadleg losses revealed that the differences were within acceptable limits. The largest discrepancy was 10%, observed for pipe section J2-J3. This indicates a reasonably high degree of accuracy in the experimental setup and analysis methodology. The research also looked at the total system heat loss, comparing the results from computer simulations against the experimental data from the simulation rig. The computer results encompassed the entire hot water pipe system, while the experiment focused solely on deadleg lengths (0-J5). The comparison showed that the computer simulation consistently resulted in higher total system heat loss values. This highlights that a considerable proportion of the total energy loss (up to 46%) originates from system components not directly included in the deadleg loss simulation (0-J5). The acceptable agreement between the calculated and experimental data from various water usage patterns and tank temperatures demonstrated that the modified experimental rig achieved its objective. This supports the conclusion that the experimental methodology accurately captured heat loss in the targeted sections of the system.
3. Implications of the Comparison for Domestic Hot Water Systems
The findings suggest that a substantial portion of the overall heat loss in a domestic hot water system originates from sources beyond the simulated deadleg sections. This implies that optimizing insulation and pipe design beyond the immediate deadlegs can considerably improve energy efficiency. The acceptable level of agreement between calculated and experimental results demonstrates the effective design and function of the experimental setup in simulating real-world heat loss phenomena. By multiplying the calculated and experimental daily heat losses per meter by the respective deadleg lengths, the researchers obtained daily deadleg losses for each section (data presented in tables for high and low tank temperatures). The results provided valuable insights into the magnitude of deadleg losses under varying operational conditions and highlighted the importance of accurate modeling to optimize energy efficiency in domestic hot water systems. The study successfully demonstrated the applicability of the experimental methods for assessing the efficiency of existing domestic hot water systems and informing design improvements.
V.Challenges and Future Improvements
The study highlighted challenges related to the air-conditioning unit. During summer experiments, ice formation on the evaporator fins due to high humidity reduced the cooling capacity of the system. To address this, the researchers suggested using a dehumidifier to improve the performance and reliability of the heat transfer simulation. The report also noted that the insulation of pipe fittings caused some inconsistencies in temperature readings among thermocouples. This led to the use of only the middle thermocouple readings for determining average water temperature to improve the accuracy of heat loss calculation.
1. Air Conditioning Unit Limitations Ice Formation and Humidity
One significant challenge encountered during the summer experiments was ice formation on the evaporator fins of the air-conditioning unit. This issue stemmed from the laboratory room temperature being higher than the air supply temperature to the refrigeration system, resulting in a higher dew point temperature. The ice buildup gradually lowered the supply cool air temperature, affecting the accuracy of the heat loss simulation. While adjusting the expansion valve pressure could mitigate this, it was already operating at its upper limit. This limitation emphasizes the importance of environmental control when conducting precise heat transfer experiments. The issue highlights the need for improved environmental control, potentially through incorporating a dehumidifier to regulate moisture content in the supply air to the air-conditioning unit. This would prevent ice formation and maintain the accuracy of the simulated ambient temperature, thereby enhancing the reliability of the experimental data related to deadleg losses.
2. Thermocouple Placement and Temperature Measurement Accuracy
The placement of thermocouples also presented a minor challenge. While three thermocouples were installed on each pipe section to obtain a representative average temperature, the insulation effect of the fittings at each pipe end sometimes resulted in the end thermocouples recording slightly higher temperatures than the middle thermocouple. To address this inaccuracy, the researchers opted to use only the middle thermocouple reading as a measure of the mean water temperature. This decision, although simplifying the analysis, highlights potential limitations in temperature measurement. Future experiments could benefit from improving thermocouple placement or employing more sophisticated temperature sensing methods to capture the temperature profiles along the pipe more accurately. Improving the accuracy of temperature readings is crucial for accurate determination of heat transfer coefficients and heat losses in future studies related to deadleg losses in domestic hot water systems.