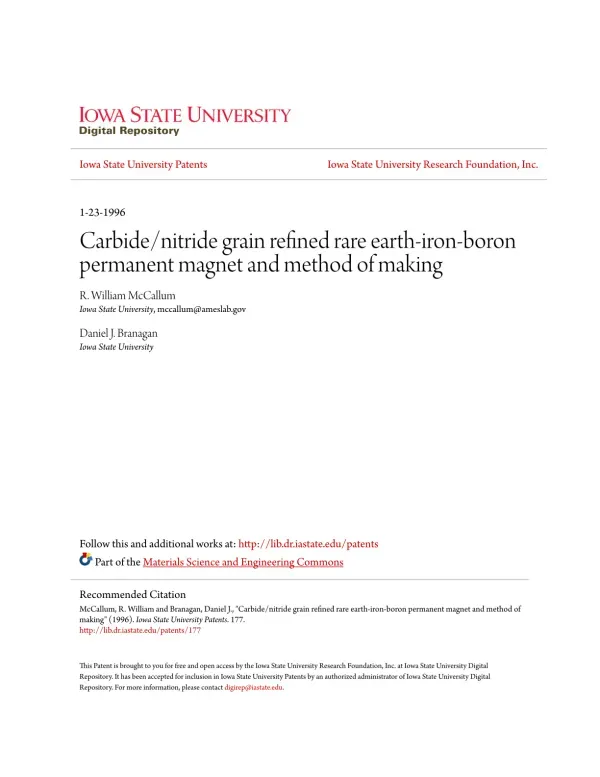
Rare Earth Magnet Manufacturing
Document information
Author | R. William McCallum |
School | Iowa State University |
Major | Materials Science and Engineering |
Document type | Patent |
Language | English |
Format | |
Size | 1.49 MB |
Summary
I.Abstract Carbide Nitride Grain Refined Rare Earth Iron Boron Permanent Magnets
This patent describes a novel method for producing high-performance rare earth-iron-boron (RE-Fe-B) permanent magnets. The process involves creating a melt of RE, Fe/Co, and B, adding a transition metal (TR) like Ti, Zr, or Hf, and C/N to form stable carbide/nitride compounds. Rapid solidification creates amorphous particulates with dispersed TRC, TRN, or TRCN precipitates. Subsequent heating nucleates and grows an optimal grain size of the hard magnetic phase, with further precipitate formation at grain boundaries. Finally, elevated temperature consolidation shapes the permanent magnet, with the precipitates pinning grain boundaries to prevent detrimental growth and enhance magnetic properties. This innovative method leads to improved grain refinement resulting in superior magnet performance.
1. Melt Preparation and Alloy Composition
The core of the patented method for creating carbide/nitride grain refined rare earth-iron-boron permanent magnets begins with the meticulous preparation of a molten alloy. This melt constitutes a base alloy composition comprising rare earth elements (RE), iron (Fe) and/or cobalt (Co), and boron (B). The specific composition of the rare earth elements is not explicitly defined, allowing for flexibility in material selection. Crucially, a transition metal (TR) is introduced. This TR is selected from at least one of Ti, Zr, Hf, V, Nb, Ta, Cr, Mo, W, and Al. Simultaneously, at least one of carbon (C) and nitrogen (N) is incorporated into the molten alloy in substantially stoichiometric quantities. The purpose of this precise addition of the transition metal and either carbon or nitrogen is the formation of a thermodynamically stable compound, such as a TR carbide, nitride, or carbonitride. The presence of these compounds is vital for the subsequent stages and serves as a foundation for achieving the desired grain refinement and enhanced magnetic properties in the final product. This initial melt creation is a pivotal step in the patented permanent magnet manufacturing process.
2. Rapid Solidification and Amorphous Structure Formation
Following the creation of the base alloy melt with the added transition metal and carbon/nitrogen components, the next crucial step involves rapid solidification. This technique is employed to transform the molten alloy into particulates exhibiting a substantially amorphous, or metallic glass, structure. The rapid cooling process inhibits the formation of large, ordered crystalline structures, instead resulting in a non-crystalline arrangement of atoms. Concurrently, the rapid solidification process leads to the dispersion of primary TRC, TRN, and/or TRCN precipitates within this amorphous matrix. These primary precipitates, consisting of the thermodynamically stable compounds formed from the transition metal and carbon/nitrogen, are finely distributed throughout the amorphous material. Their presence and distribution are key factors in influencing the microstructure and subsequent magnetic properties of the final permanent magnet. The amorphous structure and dispersed precipitates established during this stage provide the ideal starting point for the next phase of processing, which involves crystallization and grain growth control.
3. Crystallization Grain Growth Control and Secondary Precipitate Formation
The amorphous particulates generated during rapid solidification are then subjected to a carefully controlled heat treatment. This process is designed to elevate the temperature above the crystallization temperature of the base alloy composition. This thermal treatment facilitates the nucleation and growth of a hard magnetic phase within the particulates, achieving an optimal grain size. Importantly, the heat treatment also results in the formation of secondary TRC, TRN, and/or TRCN precipitates. These secondary precipitates preferentially locate at the grain boundaries of the growing hard magnetic phase. The precise control of grain size is paramount to achieving optimal magnetic properties in the final permanent magnet. The interplay between the primary and secondary precipitates and their location at grain boundaries plays a critical role in the subsequent stages of processing and the final magnetic properties. This stage sets the stage for the final consolidation and shaping of the rare earth-iron-boron magnet.
4. Consolidation and Grain Boundary Pinning
The final step in the fabrication of the carbide/nitride grain refined rare earth-iron-boron permanent magnet involves consolidation. The crystallized particulates, now possessing the desired hard magnetic phase with the strategically placed primary and secondary precipitates, are consolidated at an elevated temperature. This process transforms the particulate material into a shaped object, the final permanent magnet. The presence of both primary and secondary TRC, TRN, and/or TRCN precipitates acts as a crucial mechanism for pinning the grain boundaries during this high-temperature consolidation. This grain boundary pinning effectively inhibits the typically detrimental grain growth, which would otherwise negatively impact the magnetic properties. By preventing excessive grain growth, the magnetic properties of the final permanent magnet are enhanced. This carefully controlled consolidation process is essential in realizing the superior performance characteristics of this patented method for producing high-performance permanent magnets.
II.Method of Making Optimizing Grain Size and Magnetic Properties
The patented method centers on a two-step process. First, a melt containing rare earth elements (RE), iron (Fe) or cobalt (Co), and boron (B) is created. Transition metals (TR) – such as Ti, Zr, Hf, V, Nb, Ta, Cr, Mo, W, or Al – along with carbon (C) and/or nitrogen (N) are added to the melt to form thermodynamically stable carbide, nitride, or carbonitride compounds. Rapid solidification of this melt produces amorphous particulates containing primary TRC/N precipitates. The second step involves heating these particulates above the crystallization temperature to grow the hard magnetic phase to an optimal grain size. This heat treatment also leads to the formation of secondary TRC/N precipitates at grain boundaries. These precipitates play a crucial role in pinning grain boundaries during subsequent high-temperature consolidation, minimizing grain growth which is detrimental to the magnetic properties of the final product. The result is a denser, higher-performing permanent magnet.
1. Melt Creation and Alloy Composition Foundation for Permanent Magnet Production
The process begins by forming a melt with a base alloy composition. This composition includes rare earth elements (RE), iron (Fe) or cobalt (Co), and boron (B). The precise ratios of these elements are not explicitly detailed in the abstract, suggesting some flexibility in the recipe for rare earth magnets. However, the addition of a transition metal (TR) from the group Ti, Zr, Hf, V, Nb, Ta, Cr, Mo, W, and Al, is critical. Alongside the transition metal, either carbon (C) or nitrogen (N), or both, are introduced in substantially stoichiometric amounts to form thermodynamically stable compounds—carbides, nitrides, or carbonitrides. This initial melt composition is the bedrock of the process. The careful balance of these elements, with particular emphasis on the formation of these stable compounds, directly impacts the microstructure and thus the final magnetic properties of the resultant permanent magnet. The creation of this precisely controlled melt is the crucial first step in optimizing grain size and overall magnet performance.
2. Rapid Solidification Creating an Amorphous Precursor for Grain Refinement
The next stage involves the rapid solidification of the carefully prepared melt. This rapid cooling process is key to achieving an amorphous, or metallic glass, structure within the resulting particulates. This non-crystalline structure is essential for subsequent grain refinement. The rapid cooling prevents the formation of large crystals, which would hinder the desired fine-grained microstructure. In this amorphous state, primary TRC, TRN, or TRCN precipitates are dispersed throughout the material. The distribution and characteristics of these precipitates within the amorphous phase are crucial to subsequent processing and the optimization of the final magnetic properties. This rapid solidification step lays the foundation for the precise control of grain size that is central to achieving superior performance in the final permanent magnet. The fine dispersion of precipitates within the amorphous structure is vital for the later stages of heat treatment and consolidation.
3. Heat Treatment Nucleation Growth and Secondary Precipitate Formation for Enhanced Magnetic Properties
Following rapid solidification, the amorphous particulates undergo a heat treatment process. This involves heating the material above its crystallization temperature. This heat treatment initiates the nucleation and growth of a hard magnetic phase. The aim is to achieve an optimum grain size, a critical factor influencing the magnetic properties of the finished product. Importantly, the heat treatment also results in the formation of secondary TRC, TRN, or TRCN precipitates. These secondary precipitates strategically locate at the grain boundaries of the hard magnetic phase. The presence of these precipitates at the grain boundaries, in combination with the primary precipitates already present from the rapid solidification step, is critical for the next stage. They help control the grain growth during consolidation, leading to significant improvements in the overall magnetic properties of the final permanent magnet. This carefully controlled heat treatment is paramount to optimizing the microstructure and resultant performance.
4. Elevated Temperature Consolidation Achieving Final Shape and Optimized Magnetic Properties
The final step involves consolidating the heat-treated particulates at an elevated temperature. This process transforms the material into a shaped permanent magnet. The primary and secondary precipitates, formed in earlier stages, play a vital role in this final stage. They act to pin the grain boundaries, preventing excessive grain growth that is detrimental to the magnetic properties. The successful control of grain growth during consolidation is directly attributable to the presence and distribution of these precipitates. The suppression of excessive grain growth directly translates into enhanced magnetic properties within the finished permanent magnet. This consolidation process, combining high temperature and the pinning effect of the precipitates, is the final critical step in realizing the superior performance of the patented method for producing high-quality, high-performance rare earth-iron-boron permanent magnets.
III.Inventors and Assignee
The inventors listed on the patent are R. William McCallum and Daniel J. Branagan, both affiliated with Iowa State University. The assignee is Iowa State University Research Foundation, Inc. The patent application number is 232,837, filed on August 25, 1994.
1. Inventors of the Carbide Nitride Grain Refined Rare Earth Iron Boron Permanent Magnet Technology
The patent application lists two inventors: R. William McCallum and Daniel J. Branagan. Both inventors are affiliated with Iowa State University, highlighting the university's role in the development of this novel permanent magnet technology. The email address [email protected] is provided for R. William McCallum, suggesting a connection to the Ames Laboratory, a U.S. Department of Energy national laboratory. While the exact nature of their contributions is not specified within this section, their involvement points to the research and development efforts that led to this innovative method for producing high-performance rare earth magnets. The expertise of these inventors in materials science and magnetic materials is implicit given the nature of their invention and its complexity. Their affiliations with a renowned university and national laboratory underscore the scientific rigor behind the patented technology.
2. Assignee and Intellectual Property Rights
The assignee of this patent, meaning the entity that owns the intellectual property rights, is the Iowa State University Research Foundation, Inc. This indicates that the foundation, a non-profit organization, holds the rights to license and commercialize this technology for manufacturing carbide/nitride grain refined rare earth-iron-boron permanent magnets. This assignment is common practice for universities to manage and benefit from inventions arising from research conducted at their institutions. The involvement of the foundation points towards a strategic plan for transferring research outcomes from academia to industry, potentially leading to the widespread adoption of this innovative magnet manufacturing method. The application number 232,837 and filing date of August 25, 1994, provide crucial information for tracking the progress and status of this intellectual property.