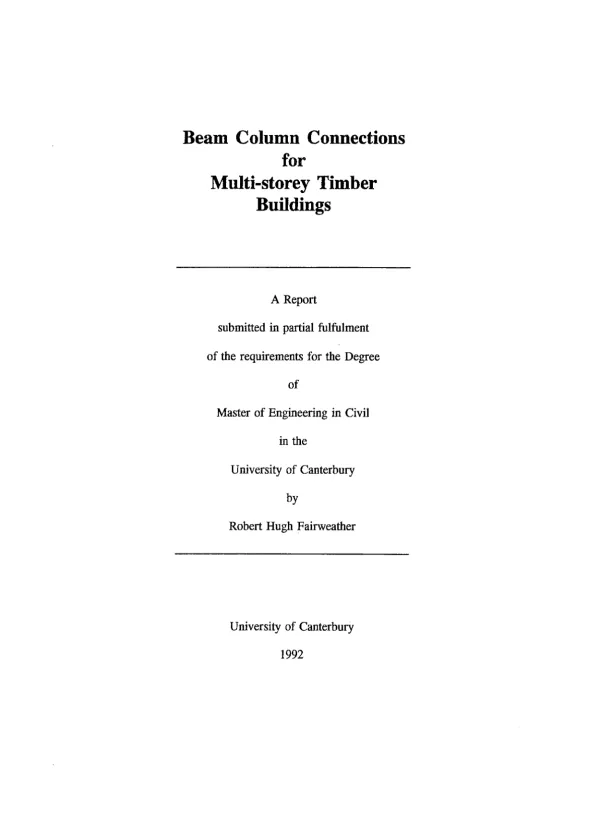
Seismic Timber Beam-Column Joints
Document information
School | University of Canterbury |
Major | Civil Engineering |
Document type | Report |
Language | English |
Format | |
Size | 7.39 MB |
Summary
I.Testing of Epoxy Bonded Steel Dowel Connections in Glulam Timber under Simulated Seismic Loads
This research investigated the performance of eight different beam-column connections in glulam timber using epoxied steel dowels. Three connection types were tested: epoxied steel dowels only; epoxied threaded rods connected to a prefabricated steel hub; and epoxied threaded rods bolted to steel side brackets. Two bar types (mild steel deformed reinforcing bars and high-strength threaded rods) and two epoxy types were also compared. The tests simulated seismic loads using quasi-static cyclic loading, measuring displacements, shear forces, and stresses. The goal was to assess the suitability of these moment-resisting connections for multi-storey timber buildings in New Zealand.
1. Connection Types and Test Setup
The study involved testing eight glulam timber connections using epoxy-bonded steel dowels under simulated seismic loads. Three distinct connection types were examined: 1) connections with epoxied steel dowels only; 2) connections using epoxied threaded rods embedded in the timber members and bolted to a prefabricated steel hub; and 3) connections with epoxied threaded rods bolted to two steel side brackets flanking the column. Two types of steel bars were used: mild steel deformed reinforcing bars and high-strength threaded rods. The researchers also investigated several bar arrangements within the joints, two sizes of deformed bars, and two different epoxy types. This comprehensive approach aimed to evaluate the effectiveness of various design parameters on the overall performance of these connections under seismic stresses. The use of multiple connection types, bar types, and epoxy types ensures a robust assessment of their structural capabilities.
2. Materials and Sponsors
The successful completion of this project relied heavily on material and financial support from various organizations. All glulam timber was generously donated by three prominent New Zealand manufacturers: Hunter Laminates Ltd (Nelson), Peter Stevens Ltd (Christchurch), and McIntosh Timber Laminates Ltd (Auckland), acting under the auspices of the Structural Engineered Timber Manufacturers Association (SETMA). The epoxy used in the tests was donated by Adhesive Technologies Ltd (Auckland) and Hylton Parker Fasteners (Christchurch). Financial backing was secured through scholarships awarded by the Timber Design Society (Pacific Timber Engineering Scholarship) and the New Zealand National Society for Earthquake Engineering (Earthquake Engineering Research Scholarship). This collaborative effort highlights the importance of industry partnerships in advancing research and development in the field of structural timber engineering, emphasizing the widespread interest in improving the design and performance of timber structures.
3. Epoxy Bonding Method and Recent Applications
A key focus of the research was the novel epoxy bonding technique used to embed steel dowels into the glulam timber. This involved drilling a hole slightly larger than the dowel diameter, carefully centering the bar, and injecting epoxy into a grout hole at one end until it flowed out of an air hole at the opposite end. This technique allows for the placement of steel bars at both the top and bottom of the beams, creating a compression/tension couple that resists column moment, with shear being carried by dowel action. This system shows promise as it protects steel from corrosion, provides fire protection for the structural connection due to the surrounding glulam, and provides a visually appealing, concealed fastening system. In New Zealand, examples of this innovative technique include swimming pools (Buchanan and Fletcher, 1989) and a space frame roof (NZ Journal of Timber Construction, 1986). The success of these previous applications underscores the potential for wider adoption of this method.
4. Addressing the Need for Improved Connections in Multi Storey Timber Buildings
The research is driven by a clear need for more information on the design and performance of moment-resisting connections suitable for multi-storey timber buildings. Currently, there's a significant lack of such information in New Zealand, coupled with restrictive design codes. This has resulted in limited construction of buildings exceeding two stories. However, recent studies (Halliday, 1991 and Thomas, 1991) suggest that multi-storey timber buildings up to six stories are both technically feasible and economically viable. The development of effective and efficient moment-resisting connections is therefore crucial to unlocking the potential of taller timber structures and addressing the current limitations imposed by existing design standards and a lack of readily available data. The research directly addresses this gap by providing critical data on the performance of various connection types.
5. Constructability Advantages of Steel Bracket Connections
The utilization of steel brackets and epoxied steel dowels offers significant advantages in terms of constructability. The process involves drilling holes, placing the bars, and gluing them in place at the factory. The assembled members are then transported to the construction site and bolted to the prefabricated steel bracket. This method contributes to substantially faster construction times. Well-designed connections of this type exhibit excellent ductile behavior, with final failure typically involving damage to the steel flange plates rather than the rods or timber members. A capacity design approach should be adopted to ensure the desired failure mechanism is achieved. This approach provides considerable savings in construction time thanks to quicker member erection. Examples of buildings utilizing glulam members with concrete or masonry lateral load resistance are the Carter Holt building (Auckland) and the Odlins building (Wellington) (Smith, 1982).
II.Materials and Methods
All glulam timber was donated by three New Zealand manufacturers: Hunter Laminates Ltd (Nelson), Peter Stevens Ltd (Christchurch), and McIntosh Timber Laminates Ltd (Auckland), under the auspices of the Structural Engineered Timber Manufacturers Association (SETMA). Epoxy was donated by Adhesive Technologies Ltd (Auckland) and Hylton Parker Fasteners (Christchurch). Two epoxy systems were utilized: WEST System Z105/Z205 and Hilti HIT C100. The timber used was untreated radiata pine. Steel dowel holes were drilled using a handheld air drill, and the bars were centrally placed and epoxy injected. Testing involved a quasi-static cyclic loading system with load cells, strain gauges, and high-resolution displacement measurement tools. Data was recorded by a 104 channel Burr Brown Data Acquisition System.
1. Timber Sourcing and Specifications
The glulam timber used in the study was provided by three New Zealand manufacturers: Hunter Laminates Ltd (Nelson), Peter Stevens Ltd (Christchurch), and McIntosh Timber Laminates Ltd (Auckland). This collaboration was facilitated by the Structural Engineered Timber Manufacturers Association (SETMA). Two beam sizes (90 x 495mm and 135 x 495mm) and a column with nominal dimensions of 180 x 495mm were utilized. The glulam was specified as untreated radiata pine, meeting or exceeding No.1 framing grade, with a moisture content between 12% and 16% and no pith in the outer laminations. The specifications ensured consistent material quality across the test specimens. This donation of materials significantly contributed to the feasibility of the research project, highlighting the industry's commitment to advancing glulam timber applications.
2. Epoxy Selection and Properties
The epoxy used in the tests was donated by Adhesive Technologies Ltd (Auckland), a part of Gougeon Brothers, Inc. After consultation, the WEST System Z105/Z205 two-component epoxy was chosen as the primary epoxy for its high strength, fast cure time, suitability for timber bonding, and resistance to water penetration. This epoxy was designed specifically for use with timber and exhibits optimal hardness and excellent cohesive properties. Two types of hardeners were available for the Z105 resin: the Z205 fast hardener and the Z206 slow hardener, both mixed in a 5:1 ratio. The fast hardener was preferred for its rapid cure. Additionally, a Hilti HIT C100 injection technique, donated by Hylton Parker Fasteners of Christchurch, was used for a subset of tests. This epoxy, designed for anchor fastening in damp environments, employed a modified epoxy acrylate-based synthetic resin mortar. The selection of these epoxy systems allowed for a comparison of performance characteristics.
3. Steel Dowel Preparation and Installation
Dowel holes were drilled into the timber using a hand-held air drill with a wood auger. Two auger sizes were employed: 22mm holes for D16 bars and 26mm holes for D20 bars and 3/4" BSW threaded rods. Two 8mm diameter pilot holes were drilled 30mm from each dowel hole end; one for epoxy injection and the other for air escape. The assembly method varied depending on the joint type. Precision and skill were essential, particularly when drilling through the column to fix beam positions. Larger holes could improve tolerances but would reduce column strength. Beam ends were required to be square to ensure proper contact and prevent epoxy leakage. In the case of prefabricated steel brackets, threaded rods were centered in predrilled holes, rubber seals were used, and the bracket was tightly aligned against the beam and column ends to prevent epoxy leakage. The detailed procedure ensured accurate and consistent installation of the steel dowels for the test specimens.
4. Testing Methodology and Data Acquisition
The testing program consisted of eight specimens, with four of the first connection type and two each of the other two types. Quasi-static cyclic loading was applied horizontally at the top of the column using a hydraulic jack. Load cells measured the applied load, strain gauges measured shear forces in the beams, and a high-resolution potentiometer measured column displacement. Clip gauges measured joint distortion and beam displacements relative to the column. A 104-channel Burr Brown Data Acquisition System recorded data at selected intervals, and continuous load versus deflection plots were produced using an X-Y recorder. This comprehensive testing methodology allowed for detailed analysis of the connection’s response to simulated seismic actions, providing a complete picture of its structural behavior and failure characteristics.
III.Results and Discussion of Type A Joints Epoxied Steel Dowels
All Type A connections were loaded to failure, with failures occurring in the wood, either in the beams or the joint region. No pullout of the epoxied steel bars occurred. Stresses at first cracking were generally below code-permissible values for No.1 framing grade radiata pine glulam timber. Unit 8, where bars were debonded near the beam-column face to increase bar yielding, showed excellent ductile behavior up to a displacement ductility factor of ±6. This debonding changed the shear transfer mechanism from shear to flexure of the reinforcement. Poor timber quality (presence of pith and finger joints) in Unit 8 negatively impacted performance.
1. Overall Failure Modes of Type A Connections
All Type A connections, utilizing only epoxied steel dowels, were tested to failure. Consistently, failure occurred within the wood itself, manifesting either as flexural failure in the beams (Units 2 and 8) or a combination of flexural and shear failure in the joint region (Units 1 and 3). Critically, no instances of steel dowel pullout were observed. The stresses in the wood at the initial appearance of cracks generally remained below the code-allowable values for No. 1 framing grade radiata pine glulam timber. This observation is attributed to the complex stress distribution patterns surrounding the reinforcing bars. In Unit 8, however, wood failure was likely caused by poor bonding of the steel to the timber. The consistent wood failure, despite stresses initially being below code limits, suggests potential areas for improving the design and installation procedures to enhance durability.
2. Analysis of Unit 8 Debonded Bars and Ductile Behavior
Unit 8 stands out due to its unique configuration: five D16 mild steel deformed bars epoxied into 22mm holes, with four bars in the outer laminations and one at the centroid. Crucially, each bar was deliberately debonded over a 40mm length (20mm into both the column and beam) using insulation tape. This debonding was intended to increase the length over which bar yielding would occur, promoting ductile behavior. The initial stiffness was 1.48 kN/mm, and the unit exhibited excellent ductile behavior up to a displacement ductility factor of ±6 before the test was stopped due to beam cracking. Load-deflection plots showed relatively ‘fat’ hysteresis loops, confirming that bar yielding extended into the joint core. The large sliding shear component, the small joint shear distortion, and the significant increase in beam hinge rotation due to bar yielding were key observations. Despite this ductile behavior, the test results also pointed to poor timber quality within the joint as a significant factor influencing the overall performance.
3. Comparison of Calculated and Measured Deflection Components
For several units, including Unit 8, a comparison was made between calculated and measured deflection components. In Unit 8, calculated components were underestimated at higher ductility levels but showed good agreement during elastic loading. The discrepancy between calculated and measured values increased linearly with load, suggesting that the assumed modulus of elasticity might be too low. In other Type A joints, a similar analysis showed that the sliding shear component was negligible, while joint distortion was a major contributor to deflection, particularly near failure. This discrepancy between calculated and measured values highlights the complexities of accurately modeling the behavior of these connections and suggests a need for further refinement of analytical models to more accurately predict real-world performance. The data obtained provided valuable insights for improving future prediction models.
4. Summary of Type A Joint Performance and Influence of Timber Quality
Across all Type A connections, failure consistently involved wood failure, either in the beams through flexure or in the joint region via a combination of flexure and shear. No instances of steel bar pullout were observed. Stresses at first crack initiation generally fell below code-prescribed values for No. 1 grade radiata pine glulam timber, likely due to the complex stress distribution around the reinforcing bars. However, the influence of timber quality is paramount; Unit 8’s failure was exacerbated by poor timber quality (pith and finger joints in outer laminations). The standard for glulam timber manufacturing (NZS 3606: 1981) prohibits pith in the outer laminations of No. 1 framing grade timber. The findings emphasize the critical role of high-quality timber in ensuring the reliable performance of these connections, underlining the importance of quality control in manufacturing processes.
IV.Results and Discussion of Type B Joints Steel Hub and Side Brackets
Type B connections displayed two types of behavior: elastic and limited ductile. Unit 4 (steel hub) behaved elastically up to failure, while Unit 5 exhibited limited ductility. The use of high-strength washers in Unit 5 increased the flange plate stiffness, leading to timber failure before flange yielding. Unit 6, using side brackets, showed excellent ductile behavior (ductility of 8) with failure ultimately occurring in the steel flanges rather than the timber. The arrangement of bars within the steel plate significantly influenced performance, with poor bar placement leading to timber failure due to compression strut formation.
1. Steel Hub Connection Performance Units 4 5
Units 4 and 5, employing a central steel hub connection, exhibited notably different behaviors. Unit 4 displayed purely elastic behavior up to failure, which manifested as longitudinal wood splitting along the grain of the lower column. No pullout of the epoxied steel bars occurred. Unit 5, however, showed limited ductility, reaching a displacement ductility of only 2 before failure. The difference in behavior is attributed to the type of washer used; Unit 4 used mild steel washers, while Unit 5 utilized high-strength washers. The high-strength washers increased the local stiffness of the flange plates around the bolt holes, resulting in timber failure before the flange plates reached their yield load. This highlights the significant influence of seemingly minor design details on the overall performance and ductility of the connection, demonstrating the necessity of careful consideration of all design elements.
2. Side Bracket Connection Performance Units 6 7
Units 6 and 7 utilized steel side brackets. Unit 6 displayed excellent ductile behavior, reaching a displacement ductility of ±8 before the test concluded. The load-deflection plot demonstrated linear behavior up to the yield point of the flange plates. The hysteresis loops were relatively 'fat' but exhibited a pinched shape, a result of bolt hole clearances and timber crushing by the side plates in the column. Failure involved longitudinal wood splitting along the grain in the lower column, with no bar pullout. Unit 7 showed a similar failure mode, suggesting consistent performance across these specimens. The initial stiffness for Unit 6 was 1.41 kN/mm. The strong ductile behavior demonstrated the effectiveness of this design approach under large displacements.
3. Analysis of Deflection Components in Type B Joints
Analysis of the deflection components in Type B connections revealed distinct trends. In Unit 6, deformations due to joint distortion, beam and column deformations, and sliding shear increased proportionally with the applied load. Sliding shear deformations remained generally small, except at failure where they doubled. Hinge rotation increased linearly until failure, after which a dramatic increase was observed. In Unit 4, the sliding shear component had to be estimated due to a lack of appropriate gauges. The calculated components in this unit indicated that the sliding shear component was generally small, while hinge rotation of the beams and columns was large. Beam and column deformations were also substantial, with no deflection component attributed to shear distortion of the joint. These observations reinforce the influence of different joint design elements on the various components of deflection.
4. Summary of Type B Joint Performance and Influence of Bar Placement
Both Type B connections were loaded to failure, resulting in longitudinal wood splitting along the grain of the lower column. No bar pullout occurred. Stresses at initial crack formation generally stayed below code-allowable values for No. 1 grade radiata pine glulam timber, likely due to the complex stress distribution around the bars. The importance of timber quality remains a key factor, as failures often initiated at finger joints near the bars. Type B connections demonstrated two distinct behaviors: elastic (Unit 4) and limited ductile (Unit 5). The high-strength washers in Unit 5 led to the timber failing before the flanges yielded. In contrast, Unit 6 showed exceptional ductility. These varying results highlight the need for careful attention to detail in design and material selection to optimize the performance of these connections.
5. Overall Comparison of Type B Connections
The initial stiffness of the Type B connections varied; Unit 6 displayed an initial stiffness of 1.41 kN/mm, while Unit 4 had a significantly higher stiffness of 2.67 kN/mm. This difference is directly attributable to the different connection configurations, emphasizing the influence of design on overall stiffness. The interstorey drift percentages were high (approximately 2%) across all units. The connections exhibited three behavioral categories: elastic, very limited ductility, and ductile behavior. Units 1 and 4 displayed elastic behavior up to failure, Units 2, 3, and 5 showed limited ductility (up to a displacement ductility of 2), while Units 6 and 8 demonstrated excellent ductile behavior (ductility of 8 and 6, respectively). The higher ductility in Unit 8 was due to the debonding of the bars. This comparison underscores the importance of thoughtful design choices in achieving the desired performance characteristics in timber connections.
V.Overall Conclusions on Moment Resisting Connections
The study demonstrates the feasibility of using epoxied steel dowel connections for multi-storey timber buildings. Different connection designs exhibited varying degrees of ductility. The quality of the glulam timber and the precise placement of the steel dowels are crucial factors affecting the performance and strength of these connections under seismic loads. Further research is needed to refine design guidelines for achieving optimal performance in multi-storey timber structures.
1. Feasibility of Multi Storey Timber Buildings
The research concludes that multi-storey timber buildings are not only technically feasible but also economically viable, contrary to the current limited adoption in New Zealand. This conclusion is supported by previous studies (Halliday, 1991; Thomas, 1991), which indicated the potential for structures up to six storeys. The primary barrier to wider adoption appears to be the lack of design information on suitable beam-column connections, a gap directly addressed by this research. The successful testing of various moment-resisting connections using epoxied steel dowels embedded in timber provides valuable data for advancing the design of taller timber structures and overcoming existing limitations in the New Zealand building industry.
2. Performance of Epoxied Steel Dowel Connections
The study demonstrates the potential of epoxied steel dowel connections in glulam timber for moment resistance in multi-storey buildings. The tests showed that these connections can achieve both elastic and ductile behavior depending on design parameters. The use of this technique allows for the placement of steel bars at the top and bottom of the beams, creating a compression/tension steel couple which resists the moment with shear carried by dowel action. However, the study highlights the critical importance of timber quality; the presence of defects like pith and finger joints near the connections significantly affects performance and should be strictly controlled to ensure adequate structural integrity. This finding emphasizes the need for careful material selection and quality control during construction.
3. Influence of Design Parameters on Connection Behavior
The research clearly shows that several design parameters significantly influence the behavior of the connections. The type of connection (epoxied steel dowels only, steel hub, or side brackets), the type of steel bars (deformed or threaded rods), the type of epoxy, and the arrangement and debonding of the bars within the connection all affect the stiffness, strength, and ductility of the joint. For instance, debonding the bars in Unit 8 increased ductility significantly, while the use of high-strength washers in Unit 5 led to timber failure before the steel yielded, illustrating the importance of detailed design considerations to obtain the desired behavior. Further investigation is warranted to fully understand and optimize the interaction of these parameters for enhanced performance.
4. Recommendations and Future Research
The results of this study provide valuable data for informing the development of design guidelines for moment-resisting connections in multi-storey timber buildings. However, further research is necessary to refine these guidelines and address specific issues. The quality of the glulam timber is critical and needs to be consistently high to ensure optimal performance. The complex stress distribution around the reinforcing bars requires more in-depth investigation. Furthermore, further testing and refinement of analytical models is needed to improve the predictive capabilities of design tools. The study suggests that improved analytical models should be developed to better predict the behavior of these connections in various loading conditions. Continued research will enhance the understanding and safe implementation of this innovative connection system.