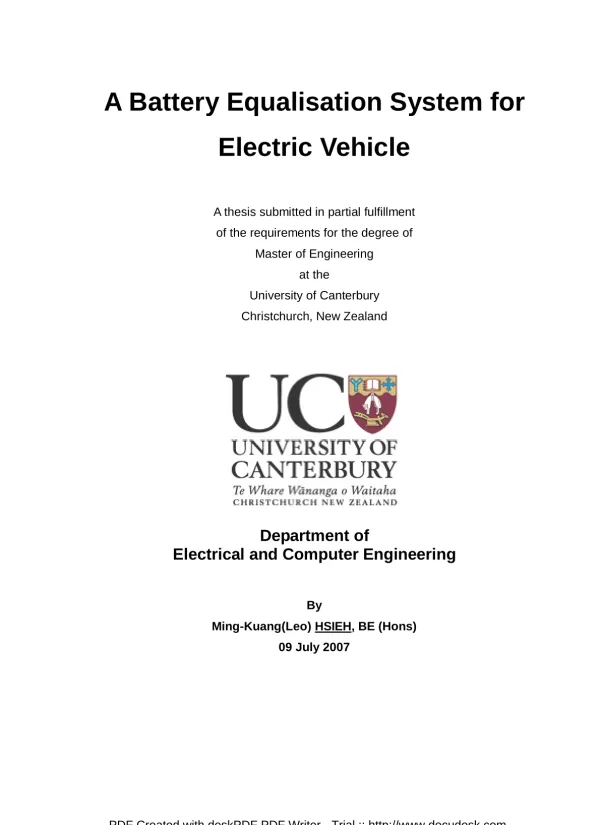
EV Battery Equalization System
Document information
Author | Ming-Kuang(Leo) Hsieh |
instructor/editor | Richard Duke, Associate Professor |
School | University of Canterbury |
Major | Electrical and Computer Engineering |
Place | Christchurch, New Zealand |
Document type | Thesis |
Language | English |
Format | |
Size | 2.45 MB |
Summary
I.Battery Equalization The Need and Solution
This thesis addresses the critical problem of battery voltage equalization in electric vehicles (EVs). Uneven charging and discharging in battery strings, due to factors like cell chemistry differences, temperature gradients, and battery age, can lead to damage and reduced lifespan. A battery equalizer actively balances the charge levels by transferring energy from higher-charged to lower-charged batteries using a high-frequency DC-DC converter. This improves EV battery life and extends the vehicle's travelling range. The project focuses on designing efficient and compact equalizers for optimal performance.
1. The Problem of Uneven Battery Charging and Discharging
The core issue revolves around the inconsistencies in charging and discharging rates within a series-connected battery string in electric vehicles. This unevenness stems from inherent differences in individual battery cell chemistry, temperature variations along the string, and the varying ages of the cells. During charging, some batteries reach their nominal voltage or a fully charged state before others in the string. If the charger continues to operate, it can overheat the fully charged batteries, shortening their lifespan. Similarly, during discharge, some batteries might reach a state of deep discharge before others, which also impacts battery life and reduces the overall vehicle's operating range. Maintaining a consistent charge level across all batteries is therefore crucial for optimal performance and extended lifespan. This is especially important for Electric Vehicles (EVs) where battery performance is directly linked to vehicle range and operational efficiency. A solution involving a battery voltage equalizer is proposed to mitigate these issues and ensure consistent battery performance.
2. Introducing the Battery Voltage Equalizer
A battery voltage equalizer is a device designed to address the problem of uneven charge distribution in battery systems. It achieves this by transferring energy from overcharged batteries to undercharged ones. The mechanism involves drawing energy from a battery with a higher charge level and then discharging that energy into a battery with a lower charge level. This energy transfer is efficiently managed using a high-frequency DC-DC converter, a common component in power electronics. Every DC-DC converter possesses its own energy storage element – this could be an inductor, a capacitor, a transformer, or a combination thereof. The switching signals controlling the converter's operation dictate how the energy storage is charged from the source (the higher charged battery) and then discharged into the load (the lower charged battery). The equalizer aims to maintain a balanced charge state across all batteries, maximizing battery life and vehicle performance. This thesis investigates different topologies for such equalizers, aiming to produce a design suitable for implementation in the EV3, the University of Canterbury's electric vehicle project.
3. Design Goals and the EV3 Project
This research project focuses on developing a battery equalizer for the EV3, a specific electric vehicle project at the University of Canterbury's Electrical and Computer Engineering Department. The EV3 is based on a Toyota MR2 chassis and uses 26 Hawker Genesis 12-volt, 26A-hour sealed lead-acid batteries connected in series to achieve a nominal 312V DC source. These batteries are physically divided into four banks due to spatial constraints within the vehicle. The design goals for the equalizer are stringent, emphasizing compactness and efficiency to minimize impact on the vehicle’s overall performance and cost. Specific requirements include small size, light weight, cost-effectiveness, easy mounting, maintenance-free operation, and high efficiency. The design must seamlessly integrate with the existing battery system without negatively impacting vehicle performance or adding substantial cost. This necessitates a meticulous design process, considering the trade-offs between various components and topologies.
II.Battery Equalizer Topologies
Three different battery equalizer topologies are analyzed: common core, common bus, and ring. The choice of topology impacts cost, scalability, and ease of implementation. The common bus topology offers flexibility for future expansion but adds cost due to extra energy storage. The common core topology is challenging for large battery strings like the 26-battery system in the EV3 (University of Canterbury's third EV, based on a Toyota MR2). The ring topology utilizes both isolated (flyback) and non-isolated (buck-boost) DC-DC converters for efficient energy transfer between battery banks and individual cells. The advantages and disadvantages of each topology are considered in the context of the EV3's specific constraints.
1. Common Core Equalizer Topology
The common core topology uses a transformer with multiple secondary windings, one for each battery or bank of batteries in the string. The primary winding is connected to the DC-DC converter, which transfers energy between batteries by adjusting the current flow in the secondary windings. The design requires careful consideration of the transformer core size and inductance to ensure even energy distribution amongst the batteries. A key challenge with this topology, especially relevant to the EV3’s 26-battery configuration, is the difficulty of implementation when dealing with a large number of batteries. The physical arrangement of the batteries (divided into four banks in three compartments) makes it complicated to implement a common core topology. Additionally, for large battery strings, a larger transformer core is needed, increasing the size and mounting complexity of the equalizer, particularly if space is limited within the vehicle.
2. Common Bus Equalizer Topology
The common bus topology uses a DC-DC converter to transfer energy between batteries via a common bus. A crucial advantage of this setup is the flexibility it offers in terms of the transformer ratio, especially beneficial for future expansion. Because the voltage rating on each side of the transformer is identical, a 1:1 transformer ratio is feasible. This means that adding or removing batteries from the string does not affect the transformer's ratio. However, a significant drawback of this topology is the necessity for an additional set of capacitors or an extra battery to act as temporary energy storage on the common bus side. This increases the overall cost and complexity of the system. This extra component requirement needs to be carefully considered against the benefits of future scalability and flexibility.
3. Ring Equalizer Topology
The ring equalizer topology employs a series connection of DC-DC converters to create a ring structure around the battery string. Non-isolated converters, such as buck-boost or Cuk converters, are used to transfer energy between adjacent batteries. The buck-boost converter offers a simpler, lower-component count design, resulting in lower manufacturing costs and a smaller physical size. While Cuk converters offer theoretically higher efficiency due to lower current ripple, this advantage is outweighed by their increased component count, especially when bi-directional energy transfer is required. The optimal choice of converter (buck-boost vs. Cuk) depends on the power levels involved. For lower power applications, the slight efficiency loss of the buck-boost is acceptable in exchange for cost savings and ease of manufacturing. The proposed design incorporates a combination of 192/144W non-isolated buck-boost converters to balance banks and 24W non-isolated buck-boost converters to balance individual batteries within banks, with a flyback converter for balancing between the top and bottom banks.
III.Converter Design and Components
The thesis details the design of three different types of converters: a 24W buck-boost converter, a 192W buck-boost converter, and a 192W flyback converter. All converters operate under current mode control with an average current of 2A. The design prioritizes compactness, low cost, ease of mounting, and high efficiency. The selection of components like the SG3526 PWM controller, specific MOSFETs (e.g., SUD35N05-26L and IR2112(S)), and inductor cores (RM core, planar inductor, integrated inductor) is discussed, emphasizing trade-offs between cost, manufacturability, and performance. The use of planar inductors is explored as a solution for space constraints. Different core materials like silicon steel, ferrite, and iron powder are compared, considering their impact on eddy current losses and frequency response. The challenges of designing for bidirectional energy transfer are addressed.
IV.Simulation and Experimental Results
Extensive simulations using PSpice are performed to validate the converter designs. A battery discharge test (30A for 60 minutes) on 8 lead-acid batteries informs the simulation parameters. Results demonstrate the effectiveness of both the 24W and 192W buck-boost converters and the 192W flyback converter in achieving battery equalization. Experimental results using the planar inductor show slightly lower efficiency compared to RM core but justify its use based on space-saving benefits. The integrated inductor shows the worst performance. Tests show that the 192W and 24W converters cannot operate simultaneously without system instability; this limitation requires further investigation in future work.
1. Simulation Methodology
Simulations were conducted using a PSpice simulator to model the performance of the designed battery equalizer. In these simulations, rechargeable batteries or battery banks were represented by 1F capacitors, while internal battery resistance and wiring resistance were modeled as 100mΩ resistors. To establish realistic parameters for the simulations, a preliminary battery discharge test was performed. This involved discharging a series-connected string of eight equally charged sealed lead-acid batteries at a rate of 30A for one hour. This discharge rate is roughly equivalent to the power consumption of the EV3 during typical city driving. The data from this test, specifically the nominal voltages of each battery after discharge, helped determine suitable initial voltage settings and voltage variation ranges for the simulation models. Each converter within the simulation was set to operate at an average current of 2A. The results of these simulations demonstrated the successful equalization of two rechargeable batteries using the proposed converter design, providing a crucial first step in verifying the theoretical design.
2. Simulation Results Buck Boost and Flyback Converters
Simulation results for the 192W buck-boost converter showed a switching waveform similar to the 24W version, with the key difference being the higher input voltage (eight times higher) leading to a correspondingly higher required MOSFET drain-to-source voltage (Vds). A current overshoot was observed in the source battery's current waveform during the switching transitions. This was attributed to the reverse recovery of the body diode in Q2. Despite this overshoot, the simulation successfully demonstrated the principle of battery bank voltage balancing. The flyback converter simulation showed that when switch VSW1 is high, Q1 turns on, charging the primary inductance. When VSW1 goes low, energy from the leakage inductance flows into a clamping circuit, and the stored energy is transferred to the secondary inductance. The simulation results confirmed the principle of balancing battery bank voltages at both ends of the battery string. These successful simulations provided confidence in the basic functionality of the proposed converter designs.
3. Experimental Results Inductor Core Comparison and Efficiency
Experimental tests were conducted to compare the performance of three different inductor cores: RM core, planar core, and integrated inductor. Three buck-boost converters were built using these cores, ensuring identical MOSFETs and PCB layouts for accurate comparison. The switching frequency ranged from 100kHz to 200kHz, and the maximum current swing was set to 6A. The results revealed that the planar inductor had an efficiency 1.5-2% lower than the RM core due to higher winding resistance resulting from the smaller cross-sectional area of the PCB track compared to the litz wire used in the RM core inductor. However, the benefit of the planar inductor's compact size for low-profile PCB design outweighed the minor efficiency loss. The integrated inductor demonstrated significantly unsatisfactory performance due to its even narrower track width, resulting in the highest DC resistance and the lowest efficiency. The planar inductor was ultimately selected for its balance of performance, ease of construction, and cost-effectiveness.
4. Experimental Results Battery Equalization Tests
Two battery equalization tests were conducted to evaluate the performance of the complete system. These tests focused on equalizing two banks of 4 x 12V batteries, using the designed 192W converters (tested at their rated capacity) under a 96W load. The tests involved initially measuring the open-circuit voltage of each battery and then creating a voltage difference between two banks by intentionally including older, weaker batteries in one bank. After a one-hour discharge at 30A (simulating typical city driving conditions for the EV3), the open-circuit voltage of each battery was measured again. The results indicated successful equalization of individual batteries to their adjacent counterparts, but also revealed limitations. Specifically, the 192W converter and the 24W converters could not operate simultaneously without causing system instability. This issue highlighted the need for a more sophisticated control system to manage the converters, and indicated that adjusting the number of batteries per bank might improve system stability, albeit at the cost of added converters and increased size/weight. The experimental results confirmed the potential of the design, while simultaneously pointing to the need for future enhancements to its control strategy.
V.Conclusion and Future Work
The thesis concludes that the proposed battery equalization system successfully equalizes individual battery voltages, improving the overall performance and extending the lifespan of the battery pack. However, the need for a comprehensive control system to manage the operation of multiple converters is highlighted as a crucial next step. This control system would dynamically determine when to activate each converter based on real-time battery voltage readings and equalization needs, enhancing system efficiency. Future work also needs to address the simultaneous operation of converters of different power ratings. The findings provide valuable insights into the design and implementation of effective battery equalization solutions for EVs. The University of Canterbury's EV3 project serves as a case study for the practical application of the developed technology.
1. Summary of Findings
The research concludes that the proposed battery equalization system effectively equalizes individual battery voltages within a string. Simulation results, using PSpice, validated the basic functionality of the 24W and 192W buck-boost converters and the 192W flyback converter, showing successful voltage balancing in principle. Experimental testing using two banks of 4 x 12V batteries under a 96W load further confirmed the individual battery equalization capabilities. However, important limitations were observed. The planar inductor, while offering a compact design suitable for the EV3, exhibited a slightly lower efficiency (1.5-2%) compared to the RM core inductor. The integrated inductor proved unsatisfactory, highlighting the importance of inductor core selection for optimal performance. A significant finding was the inability to operate the 192W and 24W converters simultaneously. This instability necessitates the development of a sophisticated control system in future work to regulate converter operation based on real-time battery voltage information.
2. Limitations and Future Research Directions
The experimental testing revealed two key limitations. First, the absence of a comprehensive control system made manual control necessary, hindering the efficiency and practicality of the equalization process. A dynamic control system is needed to accurately measure open-circuit voltages, calculate equalization requirements, and efficiently manage the switching of individual converters. Second, the simultaneous operation of the 192W and 24W converters proved unstable. This constraint significantly impacted the overall efficiency since the 24W converters had to remain inactive while the 192W converter performed its task. Potential solutions such as decreasing the number of batteries per bank to allow for parallel operation of converters are explored. However, decreasing the number of batteries in each bank would increase the number of required converters, leading to increased cost, size, and weight. Further research is crucial to address these issues. Developing a robust control system that optimizes the switching strategy and resolving the incompatibility of simultaneous converter operation would significantly improve the efficiency and overall effectiveness of the battery equalization system. This would require additional work to design an appropriate control strategy based on extensive system testing.
3. Inductor Technology and Current Sensing Considerations
While planar technology offered a space-saving solution for the buck-boost converters, it proved less suitable for the flyback converter due to the higher number of windings required. This necessitated using a RM core with litz wire for the flyback converter, highlighting that the optimal inductor technology is application-specific. Accurate current sensing, particularly crucial for the buck-boost converter design, posed challenges. The current sensing resistor's placement outside the voltage reference point necessitated a differential amplifier with a wide common-mode range. While readily available op-amps suffice for the 24W buck-boost converter, the op-amp selection for the 192W buck-boost converter is more restricted due to the voltage differences between the 12V controller and the 72V battery bank. These observations underline the design complexities and trade-offs inherent in high-performance battery equalization systems.